Automotive A B C Pillar Injection Moulds
Automobile A-pillars and B-pillars are short for body pillars. Generally, the car body has three pillars, which are the front A pillar, the middle pillar B pillar, and the rear pillar C pillar from the back. For cars, besides supporting the pillars, they also play the role of door frames. The A-pillar is between the engine compartment and the cockpit, and above the left and right rear-view mirrors, it will obscure part of your turning horizon, especially the left turning, so it is discussed more. The B-pillar is between the front and rear seats of the cockpit, which is the longitudinal bar between the two doors on both sides. It extends from the roof to the bottom of the car. From the inside, the seat belt is on the B-pillar. The C-pillars are on both sides of the rear seat headrest.
This Automobile Pillars Injection Mold cold runner have point gate, side gate, subgate, tunnel gate,banana gate, direct gate ,etc. Mold hot treatment use quencher, nitridation, tempering,etc. Surface finish of Part support Logo print,Texture,Polishing,Painting,Chrome Plating.
Name
|
Air Vents Mould
|
Mold size
|
Custom Size
|
Mould material
|
45#,50#,1.2312 ,1.2343 ESR,1.2738 HH , S136 ,NAK80 , SKD61 etc.
|
Mould base
|
LKM, HASCO ect.
|
Cavity
|
Single/multi
|
Runner
|
Hot/cold
|
Design software
|
UG, PROE, CAD, CAXA ect.
|
Mould life
|
300,000-3,000,000 shots
|
Delivery time
|
15-60days
|
Specification
|
Depends on customer's requirments
|
Shaping Mode
|
Plastic Injection Mould
|
Molding life
|
500,000-5,000,000shots
|
Delivery time
|
Short mold development cycle
|
Packing
|
Standard exporting wooden case
|
1) Receive customer's inquiry
2) We will quote guests within 24 hours
3) Confirm the order (price, payment terms, delivery date)
4) Product analysis (DFM)
5) After DFM confirmation by customer
6) Confirmation of mold design
7) Purchase steels and start machining processing
8) Inspection process
9) Mold core inspection is OK, start assembly
10) Tool tryout and deliver the samples to customer
11) Get feedback of samples from customer.
12) If there is a problem with the sample, repair the mold
13) After repaired , tryout and deliver samples to customer for confirmation again
14) After the sample is confirmed that there is no problem, the mold is arranged to be shipped
Please send 3D/2D drawing or samples to us if you have any needs, we will quote for free with a sound price.
1. We are a small and medium-sized mold manufacturing and injection molding manufacturer, and we have 16949 certification in the automotive industry, which has allowed us to surpass 90% of competitors of the same size; while we are small and medium-sized factories, we have large companies Management methods and quality inspection systems.
2. Our company has experienced 10 years of rapid development. We focus on serving the global customers in four directions: high quality, high precision, high efficiency and high cost-effectiveness. This has enabled us to win high-speed and stable rapid growth.
3. Half of the machines are high-speed and high-precision machines imported from Japan and Germany, including all aspects of mold manufacturing and injection molding production. This also allows us to be more comfortable to manufacture and challenge some high-precision and difficult products.
4. We have the ability to make your items more than 10% ahead of delivery deadlines and manufacturing costs than your existing suppliers.
5. We have a flexible and user-friendly manufacturing service conception that can meet the diverse needs of customers in different projects and in different periods. This is often impossible for large and large companies, but impossible for small companies due to capacity too.
6. We had made 4 types automotive pillar injection tools. the molds now are running well in customer molding plant for mass production.
JHS is committed to the research and development, design and manufacture
of various injection molds, and injection production, involving
industries and fields such as electronics, automobiles, communications
and household appliances.

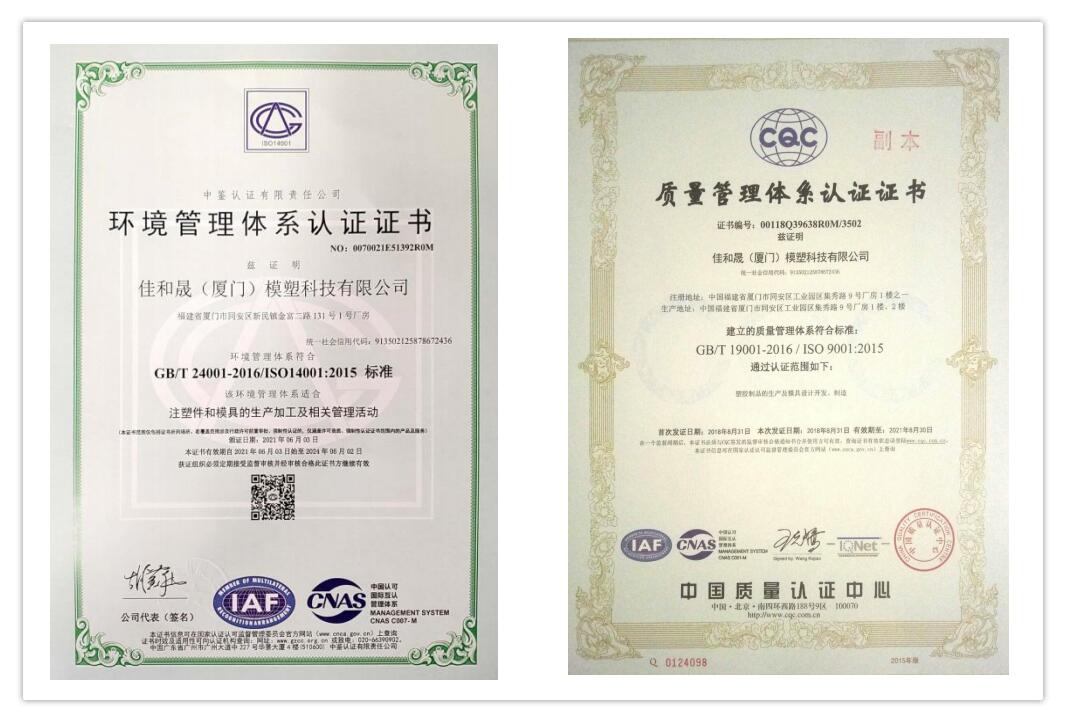

CNC Machining Workshop
|
EDM Workshop
|
Quality Inspection Department
|
Wire Cutting Workshop
|
Injection Workshop
|
Assembly Workshop
|

Q: Do you make molds for many auto parts?
A: Yes, we make molds for many auto parts, such as bumpers, reversing radar parts, car control panels, rearview mirror brackets, etc.
Q: Do you have injection molding machines to produce parts?
A: Yes, we have our own injection workshop, so we can produce and assemble according to customer requirements.
Question: What kind of mold do you make?
A: We mainly manufacture injection molds, but we can also manufacture compression molds (for UF or SMC materials) and die casting molds.
Q: How long does it take to make a mold?
A: Depending on the product size and the complexity of the parts, it is slightly different. Generally speaking, a medium-sized mold can complete T1 within 25-30 days.
Q: Can we know the mold schedule without visiting your factory?
A: According to the contract, we will send you the mold production plan. During the production process, we will update you with weekly reports and related pictures. Therefore, you can clearly understand the mold schedule.
Q: How do you guarantee the quality?
A: We will appoint a project manager to track your molds, and he will be responsible for each process. In addition, we have QC for each process, and we will also have a CMM and online inspection system to ensure that all components are within tolerance.
Q: Do you support OEM?
A: Yes, we can produce through technical drawings or samples.